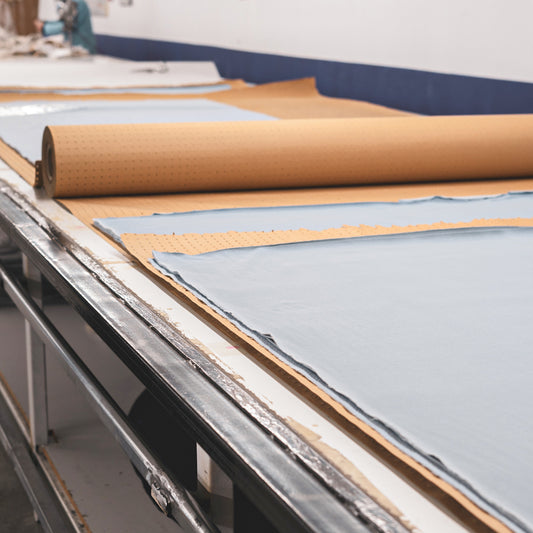
- Produktion
- Transparens
Sewing department
Welcome to our sewing department
At Elemental Coloring, we sew all our basics in our own sewing department in Turkey. When doing so we have the oppertunity to ensure the best possible quality for the product and best possible working conditions for our colleagues. At the same time, we can show you how we sew our basics - from recieving the fabric to the packaging department.
We are in daily contact with the sewing department and we prioritize visiting the facility often - preferable every quarter. We want a close and strong cooperation with our Turkish, and it works best if we are as close to the production as possible. This results in a better product, motivated employees, fewer misunderstandings, and thus fewer errors.
When we have chosen to offer chemical-free basics for the whole family, it is with the belief that the product you buy is a need to have rather then nice to have. That is why we strive to develop products with a focus on functionality and durability, which last longer than trends.
One of the many advantages of sewing all our basics in our own sewing facility is that we can sew fewer pieces at at a time. That way, we can constantly adjust our product through feedback from you, and only produce what we sell continuously. In this way, we also avoid that we will not end up with large batches of clothes that will not be sold.
We want to bring you into our value chain, including our sewing facility, and show you how our basics are made. We want to show you how it works in a professional production, where clothes are sewn every day by our colleagues, who carefully study every detail, and who are skilled craftsmen with their own specialty and skillset.
We can split the process from fabric to finished product into 3 parts
- We recieve the GOTS certified fabric from the dyehouse for a quality control of colour, shrinkage, fabric width etc. The width of the fabris is crucial when we cut the fabric later. When the fabric is approved, it is ready to go to the cutting department.
- In the cutting deparment the fabric is laid up in a predefined number of layers and lengt, based on the width of the fabric and which product we are making. This is a crucial step in order to make the most of the fabric and avoid as much waste as possible. If this process is not done adequately, there is a risk of fabric waste of 35%. The combination of our new spread machines and our basic products means that we approx. has a waste of about 5%.
The naturally colored fabric is cutted by hand by our experienced cutters, who master to cut the fabric in the exactly right pattern, that makes our basics. After the cutting process all backparts are rolled into the print department, where we print our neck prints with all the necessary information, like size, composition, and wash symbols. In this way, we aviod various hangtags, care labels, size labels, and brand labels, which are anyway cut off and thrown away as first thing. - Now the fabric is ready to be sewn to our basics. All the pieces are sorted by size, so we don't sew a size S sleeve on a size L t-shirt. From here, they are distributed to the sewing line, where each individuel product undergoes specific sewing processes. Like the sleeves that are sewn onto the front and back of a t-shirt, and the string in the hoodie that must be pulled through the hood.
When the product is finished sewing, it goes through a final check for defects befores it is packed in boxes and made ready for shipment.
To us it is important to tell and show, how and who have made our basics. Before our basics are finished sewing and packed in boxes, many of our colleagues have made sure that they fit our measurements, that the push buttons in our bodystockings sit correctly, and that the hoodie has a string in the hood.
We want to give greater insight into how our basics are made and by whom - and in that way create an increased awareness of what it takes to make chemical-free basics.
Read more journals
- Choosing a selection results in a full page refresh.